Enhancing Road Safety
History of mandatory vehicle inspection and its impact on reducing accidents.
Enhancing road safety
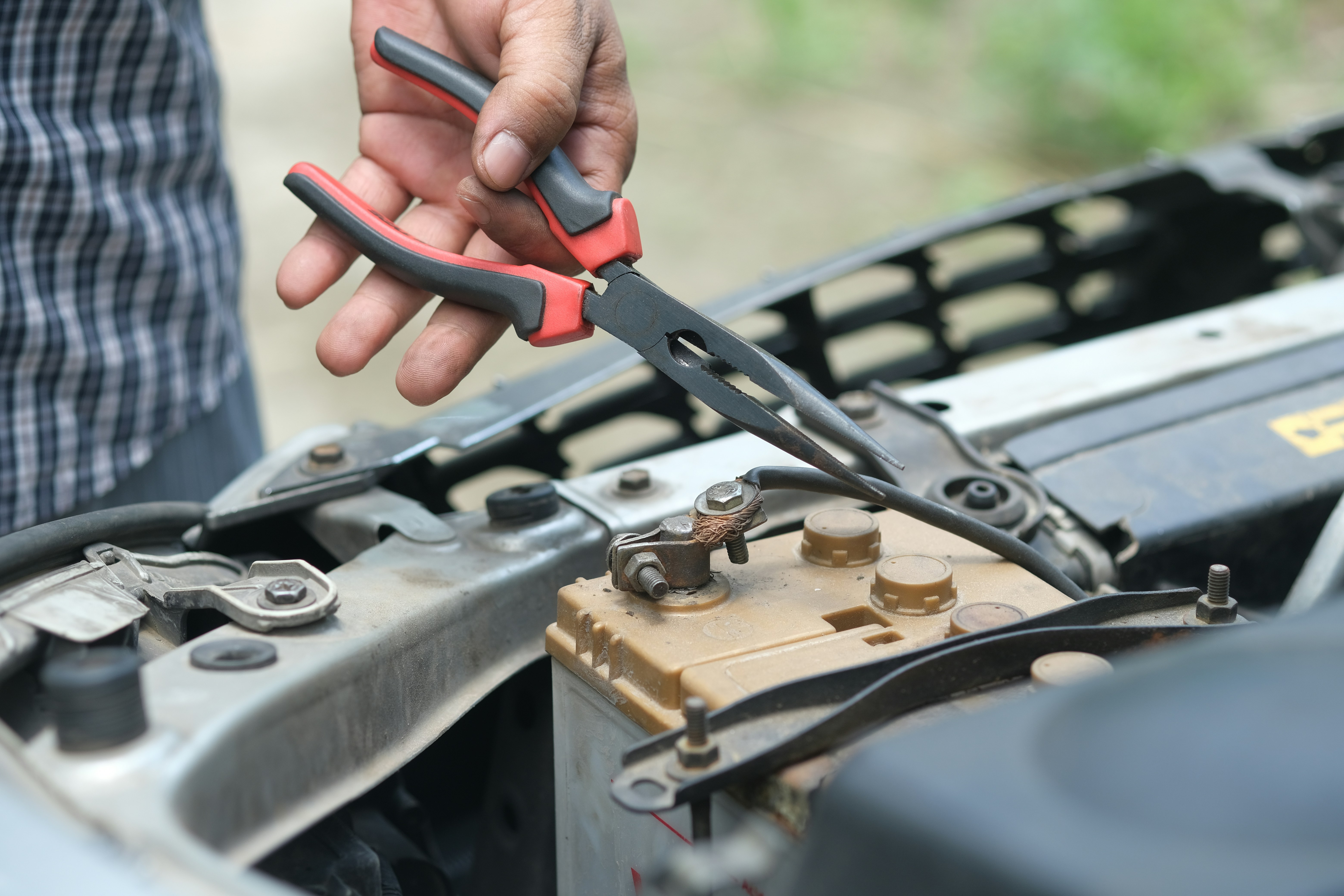
The history of mandatory vehicle inspection in Kenya represents a critical chapter in the nation's ongoing efforts to enhance road safety and reduce the devastating toll of traffic accidents. Prior to the introduction of systematic vehicle inspections, Kenya's roads were notorious for their hazardous conditions, with mechanical failures contributing significantly to the high rate of accidents. The journey toward establishing a comprehensive inspection regime offers valuable lessons for other developing nations grappling with similar challenges.
Road safety is a multifaceted challenge that requires addressing driver behavior, road infrastructure, vehicle conditions, and regulatory frameworks. Among these factors, ensuring the roadworthiness of vehicles through mandatory inspections has emerged as a critical intervention with demonstrable impact on accident rates and severity. This article examines the evolution of Kenya's vehicle inspection system, its impact on road safety, and the lessons learned that can inform similar initiatives in other contexts.
Historical Context
Kenya's first attempts at regulating vehicle safety date back to the 1970s, when basic roadworthiness checks were introduced for commercial vehicles. However, these early efforts were hampered by limited resources, inadequate technical capacity, and widespread corruption. It wasn't until the early 2000s that a more robust approach began to take shape, driven by alarming statistics that placed Kenya among the countries with the highest rates of road fatalities per capita in Africa.
The turning point came in 2012 with the establishment of the National Transport and Safety Authority (NTSA), which was given a mandate to coordinate all activities related to road safety, including vehicle inspections. Under the NTSA's leadership, Kenya implemented a modernized inspection system that incorporated digital record-keeping, standardized testing procedures, and anti-corruption measures. The system initially focused on public service vehicles, which were involved in a disproportionate number of fatal accidents, before gradually expanding to include private vehicles.
The evolution of Kenya's vehicle inspection system can be divided into three distinct phases:
- Initial Regulation (1970s-1990s): Characterized by basic inspections for commercial vehicles, limited enforcement, and minimal impact on overall road safety.
- Reform Period (2000-2012): Marked by growing recognition of the problem, policy reforms, and the establishment of new institutional frameworks to address road safety more comprehensively.
- Modernization (2012-Present): Defined by the establishment of the NTSA, implementation of digital systems, standardized procedures, and gradual expansion of inspection requirements to different vehicle categories.
Each phase has contributed to the current system, which, while still facing challenges, represents a significant improvement over the fragmented and ineffective approaches of the past.
Impact Analysis
The impact of these reforms has been significant. Data collected over the past decade shows a 28% reduction in accidents attributed to mechanical failures in vehicles that have undergone mandatory inspection. This translates to hundreds of lives saved annually and substantial reductions in the economic costs associated with road accidents, which had previously been estimated at approximately 5% of Kenya's GDP.
Accident Reduction Trend
The graph above illustrates the steady decline in accidents attributed to mechanical failures since the implementation of the modern inspection system in 2012. The trend shows a particularly sharp decrease in the years immediately following the establishment of the NTSA, with a more gradual but consistent decline in recent years. This pattern suggests that the initial reforms had a significant immediate impact, while ongoing improvements and expanding coverage have continued to yield safety benefits.
Beyond the direct safety benefits, the mandatory inspection system has catalyzed broader improvements in Kenya's automotive sector. Local garages and maintenance facilities have upgraded their capabilities to help vehicle owners meet inspection standards, creating new employment opportunities and raising the overall quality of vehicle maintenance. The inspection process has also provided valuable data on the country's vehicle fleet, informing policy decisions related to emissions standards, import regulations, and urban transportation planning.
Compliance Rates
While the impact of vehicle inspections on road safety is clear, the effectiveness of the system depends on compliance rates across different vehicle categories. The following chart illustrates the current compliance landscape.
Inspection Compliance by Vehicle Type
The data reveals significant disparities in compliance rates across different vehicle categories. Public service vehicles, which are subject to the most stringent regulations and frequent inspections, show the highest compliance rate at 85%. This is largely due to the combination of strict enforcement, regular police checks, and the commercial incentive to maintain valid certification.
Commercial trucks follow with a 72% compliance rate, reflecting the influence of both regulatory oversight and business considerations such as insurance requirements and client expectations. Private vehicles show a much lower compliance rate of 45%, highlighting the challenges of enforcing inspection requirements for individual vehicle owners who may perceive the process as inconvenient or unnecessary.
The lowest compliance rate is observed among motorcycles at 30%, despite their significant contribution to road accidents. This low rate can be attributed to the informal nature of much of the motorcycle taxi industry, limited enforcement capacity, and the practical challenges of inspecting the large and rapidly growing motorcycle fleet.
Common Issues
Vehicle inspections have revealed consistent patterns in the types of mechanical issues that contribute to road safety risks. Understanding these patterns helps target both inspection procedures and public education efforts.
Common Inspection Failures
Braking systems account for the largest proportion of inspection failures at 35%, highlighting the critical importance of this safety system and its vulnerability to wear and inadequate maintenance. Lighting issues, including non-functional headlights, brake lights, and turn signals, represent 20% of failures, significantly impacting vehicle visibility and communication with other road users.
Tire-related issues, including inadequate tread depth, improper inflation, and structural damage, account for 18% of failures. These issues directly affect vehicle handling, braking distance, and stability, particularly in adverse weather conditions. Steering system failures (12%) and emissions-related issues (10%) round out the major categories, with various other problems accounting for the remaining 5%.
This data has informed targeted public awareness campaigns and mechanic training programs focused on the most common and critical safety issues. It has also guided the development of inspection protocols that allocate appropriate time and attention to high-risk systems.
Future Directions
Colbert & Co. has been privileged to support Kenya's road safety initiatives through technical assistance, policy advisory services, and capacity building programs. Our work has focused on helping the NTSA refine its inspection protocols, develop sustainable financing models for inspection infrastructure, and design public awareness campaigns to increase compliance rates among vehicle owners.
As Kenya continues to refine its approach to vehicle safety, new challenges and opportunities are emerging. The growing number of electric and hybrid vehicles in the market requires updated inspection protocols, while digital technologies offer possibilities for more efficient and transparent inspection processes. By building on the solid foundation established over the past decade, Kenya is well-positioned to further reduce road accidents and set a standard for vehicle safety in the region.
Looking ahead, several key developments are likely to shape the evolution of vehicle inspection systems in Kenya and similar contexts:
- Mobile Inspection Units: To address the challenge of limited inspection facilities, especially in rural areas, mobile units equipped with essential testing equipment can bring services closer to vehicle owners, increasing convenience and compliance.
- Integration with Digital Vehicle Registration: Linking inspection records with vehicle registration systems can streamline administrative processes and improve enforcement by making it easier to identify non-compliant vehicles.
- Advanced Diagnostic Technologies: The adoption of more sophisticated diagnostic tools can improve the accuracy and efficiency of inspections, reducing both the time required and the potential for human error or corruption.
- Differentiated Inspection Schedules: Tailoring inspection frequency based on vehicle age, type, and usage patterns can optimize resource allocation while maintaining safety standards.
- Regional Harmonization: Coordinating inspection standards and recognition across East African countries can facilitate cross-border transportation while maintaining consistent safety levels.
These innovations, combined with continued emphasis on public education and enforcement, have the potential to build on the progress already achieved and further reduce the toll of road accidents in Kenya and beyond.
Get in Touch
Interested in improving road safety standards in your region? Our team has extensive experience in designing and implementing effective vehicle inspection systems tailored to local contexts.
Contact Us